Kit consists of 500g of PART A and 500g of PART B
Total kit volume 925ml
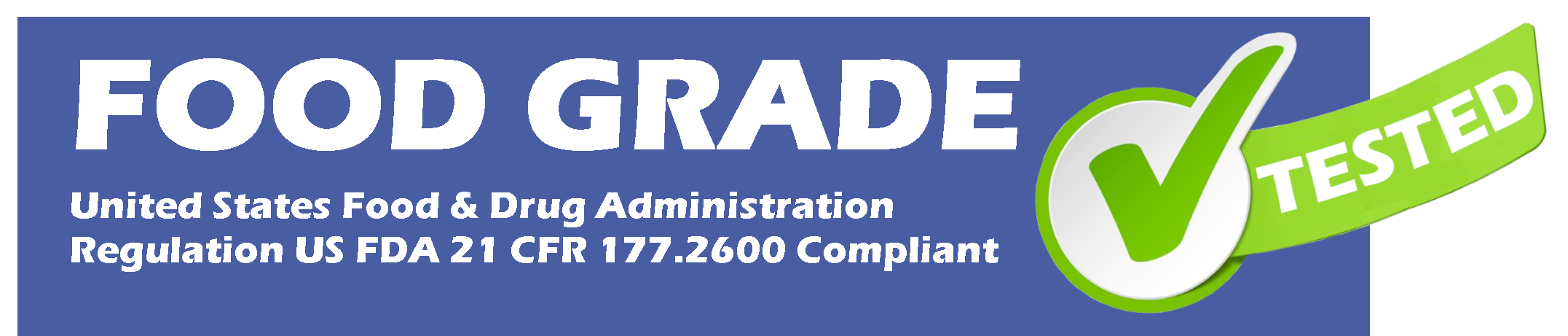
This rubber is safe for repeated contact with food and has been independently tested to verify compliance with the United States Food & Drug Administration regulation US FDA 21 CFR 177.2600.
The certificate is available to view as a PDF here
PART A and PART B are both clear liquids which are odourless and non-toxic. They react to form a translucent beige/off white coloured flexible, elastic material with high tensional and tear strength. It has outstanding release properties, a high chemical resistance and a temperature resistance of 250°C.
The two components mix easily with a simple 1:1 ratio and because of the low viscosity can be used without a vacuum chamber. There is practically no shrinkage (0.1%) and excellent reproduction of fine detail.
The pot life is approximately 8-12 minutes and the cure time is 1-2 hours.
Available in two hardnesses, soft and medium. The soft is better suited to moulding delicate, fragile items where the rubber needs to be soft and flexible enough to peel off without damaging the casting. The medium is suitable for the majority of cases.
This rubber is suitable for casting a wide range of materials including for use with confectionery, speciality foods and is safe for contact with skin for life castings. Please see below for more details. This rubber is suitable for casting a wide range of materials including for use with confectionery, speciality foods and is safe for contact with skin for life castings. Please see below for more details.
For creating a two part mould or moulding a glass object a release agent is required click here
Can be pigmented to a wide range of colours click here
It can be softened to your own requirements using this softening additive click here
Can be made thixotropic for applying to vertical surfaces or to over head objects click here
Properties | Units | Extra Soft | Soft | Medium |
---|
Pot Life (25°C) | Minutes | 10-20 | 8-12 | 8-12 |
Cure Time (25°C) | Hours | 2-4 | 1-2 | 1-2 |
Viscosity (25°C) | Mpa.s | 3000 | 5000 | 8000 |
Density (25°C) | g/cm3 | 1.08 | 1.08 | 1.08 |
Hardness | Shore A | 5 | 15 | 28 |
Linear Shrinkage | % | 0.1 | 0.1 | 0.1 |
Tear Strength | KN/m | 13 | 24 | 24 |
Elongation at Break | % | 500 | 500 | 450 |
Tensile Strength | Mpa | 2.8 | 5.5 | 6.8 |
THE FINISHED MOULD IS SUITABLE FOR USE WITH:
- Food
- Sugar craft & Confectionery
- Life casting/Body moulding
- Polyurethane resin
- Epoxy resin ( Excl. some epoxies, check with supplier of the resin if silicone moulds are suitable.)
- Polyester resin
- Acrylic resin
- Plastisol (PVC)
- Plaster
- Cement
- Polymer clays (Will inhibit the cure of liquid platinum silicone, see below)
- Waxes
- Soaps
- Metals with a pouring temperature below 250°C
*CURE INHIBITION*
A release agent will not create a sufficient barrier to prevent cure inhibition but a layer of paint will. If the paint is solvent based allow sufficient time for the solvent to completely evaporate off as that too can inhibit the cure
Great care must be taken when handling and mixing all addition-cured silicone elastomer systems. All the mixing tools (vessels and spatulas) should be clean and constructed in materials which do not interfere with the curing mechanism. The cure of the rubber can be inhibited by the presence of compounds of nitrogen, sulphur, phosphorus and arsenic; organotin catalysts and PVC stabilisers; epoxy resin catalysts and even contact with materials containing these substances e.g. moulding clays, sulphur vulcanised rubbers, condensation cure silicone rubbers, some printed plastics, onion and garlic.
Technical Data Sheet
Safety Data Sheet Part A
Safety Data Sheet Part B